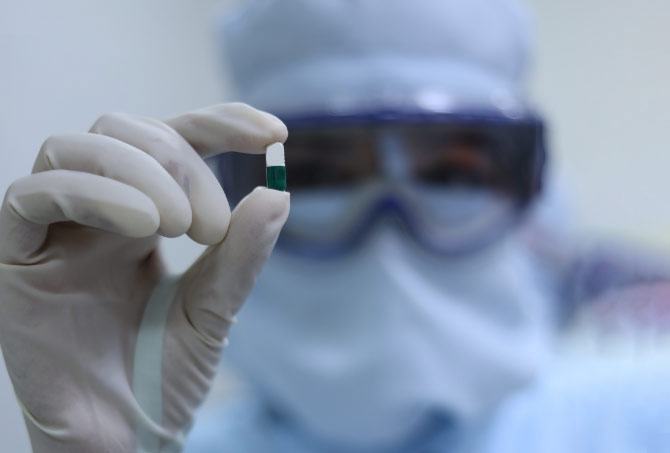
Technology is the mainstay of our manufacturing capabilities, with digital being a key pillar of our strategy. We have invested in manufacturing automation to maintain quality and productivity at the highest levels. Our plants, and the expertise of our people running them, help Lupin maintain benchmark standards in manufacturing quality.
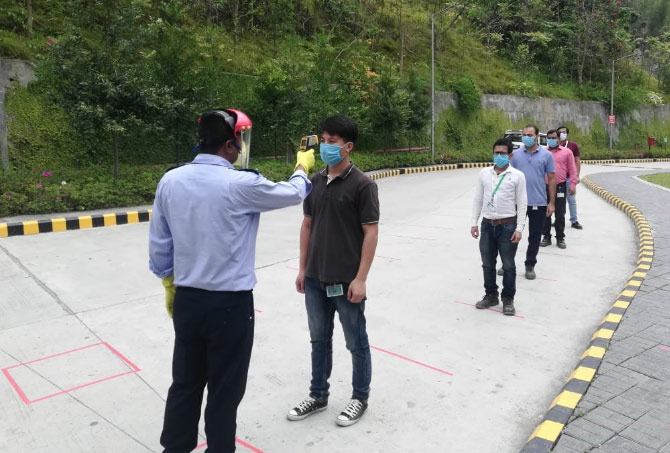
Industry best Environment, Health and Safety (EHS) practices enables Lupin to standout from competition and ensure sustainable growth. All Lupin’s plants are cGMP compliant and have made substantial investments in upgrading infrastructure to meet the constantly evolving EHS standards.
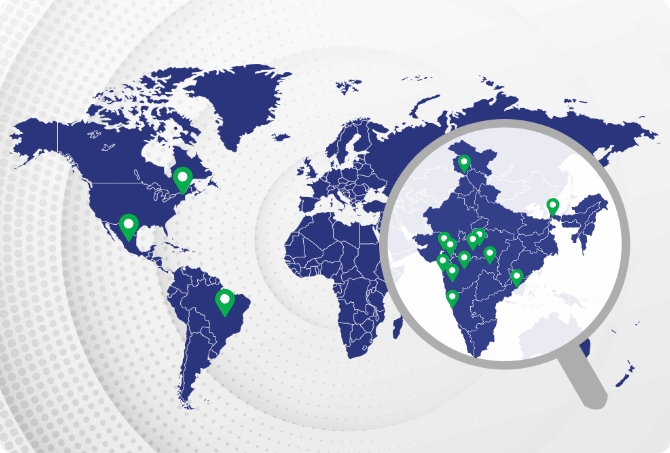
Our 15 state-of-the-art manufacturing facilities are spread across India, the United States, Brazil and Mexico. These manufacturing sites are equipped with modern production facilities and are designed to meet the required regulatory norms. Our sites are regularly inspected by national and international authorities to ensure 24×7 compliance and conformance.